Humans are always looking for ways to perform tasks quickly and flawlessly. Advancements in industrial automation and efforts to automate machine activities contribute to increased production speed and product quality. With advances in science and technology, industrial automation is expanding its boundaries day by day. For example, the creation of a machine vision system in industrial machinery has been able to solve many industrial challenges for product quality control or separation. Vision systems operate based on processing visual features such as size, shape, color, etc., in images.
Machine vision comprises essential components such as industrial cameras and image processing software sent from it. Image processing and creating algorithms to solve complex industrial problems are a very broad and fascinating field. The Vision Systems team has prepared a comprehensive machine vision and image processing training course with Halcon software for enthusiasts in this field. In the following article, we will discuss several examples of machine vision applications in industry.
Industrial Parts Quality Control System with Machine Vision
Industrial parts require the most precise quality control systems because even the smallest defect or problem in a machine part can disrupt its operation. Various types of quality control devices for industrial parts rely on machine vision. These devices operate specifically. After detecting a defective part, it is sent to the reject section, and the part is removed from the production line. In two chapters of the machine vision training course, the process of communication between Halcon image processing software and PLC for receiving reject commands is fully explained. In the video below, you can see how the quality of various parts such as screws, nuts, washers, etc., is automatically inspected.
First of all, we need to sort the parts so that we can take pictures of each of them. To detect all potential defects, we need images from various angles. Therefore, multiple cameras have been used in this device to fully cover the surrounding space of each part. In the image below, you can see the sorting stages, image processing, and separation of intact parts from left to right.
This device is capable of inspecting more than 500 parts per minute. In the image below, you can see that 4 cameras have been used to inspect the part from 4 directions (360 degrees).
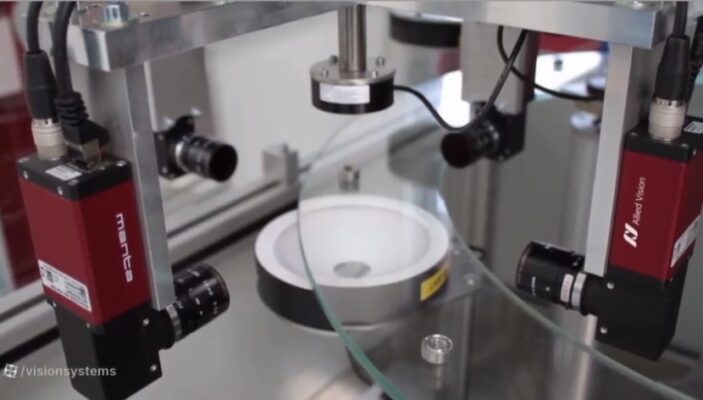
Automotive Spark Plug Quality Control with Machine Vision
Machine vision can be used to inspect various automotive parts and, after detecting faults, separate them from other parts. The spark plug is one of the sensitive parts where even the smallest defect can disrupt its proper function. In the image below, you can see different sections of an automotive spark plug; using image processing, we can inspect and control each of these sections, such as the presence of the negative electrode, gap size, base length, thread accuracy, etc.
In the video below, the quality control of automotive spark plugs is performed using a camera that views the spark plug from an angled side. With machine vision, we can detect even defects that are not easily identifiable with the naked eye. In this spark plug inspection system, back lighting is used.
The system works by sending images of the spark plugs to the image processing software by the camera. These images are compared to an acceptable sample pattern of a healthy spark plug, and if any defects are found, the defective spark plug is removed from the production line by a pick and place robot. As shown in the image below, 4 samples of defective spark plugs and their defects are compared to the pattern.
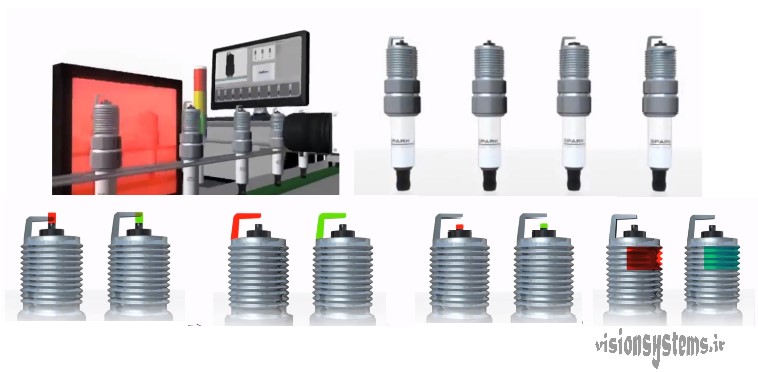
Sorting Devices with Image Processing
Sorting refers to arranging and categorizing, and sorting is a term used for categorizing and grading various products. Generally, product separation is done based on various parameters such as visual appearance, structure, dimensions, and color. With the help of image processing, we can examine the visual characteristics of various products. A device that performs sorting operations is colloquially called a sorting device. In the image below, you can see a sorting device.
Sorting devices come in various types, and each is used to categorize a specific product. Most sorting devices operate based on image processing. In this way, the product image is captured by a suitable camera and transferred to the image processing program. In the program, the image is compared with the desirable pattern, and if the image does not match the pattern minimally, the defective product is separated.
Fruit Sorting with a Camera (Color Sorter)
Quality control, grading, and proper packaging of agricultural products contribute to their longevity and wider distribution. Today, fruit and citrus sorting machines are more popular than ever among producers. These machines often use
In the image below, you can see ice cream containers. Containers with smaller sizes are removed from the line with a command to the reject section
Vision Systems: A Leading Company in Machine Vision Technology
Vision Systems, in pursuit of its goals to expand education on innovative technologies and execute industrial projects, has implemented various machine vision projects using Halcon software. The main activities of this company include implementing machine vision systems, participating in vision projects, and providing machine vision training, some of which are summarized below.
Implementation of Projects on Production Lines
One of the practical projects implemented by the Vision Systems team is the quality control of tablets in blister machines. In this system, broken, cracked, and empty tablets are detectable. This project has been implemented in a pharmaceutical factory, as shown in the image below, and is currently operational.
Consultation and Participation in Industrial Machine Vision Projects
Another service offered by us is consultation and participation in industrial machine vision projects. For example, a project was carried out in collaboration with Arka Industrial Robot Equipment Company to control the quality of rear glass elements in cars. The aim of this project is to detect cuts in the rear glass elements. The programming for this project was done by Vision Systems using HALCON software. As shown in the image below, the left image is a sample without any defects, while the right image has a crack in one of the internal elements of the glass.
Project-Based Machine Vision Training at Vision Systems
We have initiated the first industrial machine vision training course in Iran using Halcon software, conducted by a specialized team. Multiple projects such as liquid level inspection, color part separation, print control, PLC rejection, etc., have been thoroughly explained in a simulated laboratory environment with full details. Alongside training courses, specialized consultations have enabled enthusiasts in this field to carry out their projects in collaboration with the Vision Systems team.