Products that are not properly labeled or have incorrect printing of dates, prices, and barcodes can have a negative impact on a brand’s popularity or even lead to the return of goods to the factory. Machine vision systems installed on production lines are capable of inspecting labels and various packaging defects, and… commanding relevant sections to remove defective products from the production line.
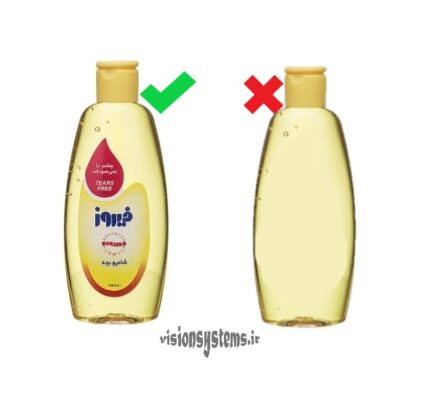
Equipment Implemented for Label Inspection Project
The main equipment in machine vision projects includes cameras, lighting, and image processing software. Here, we’ve used Basler camera models and lenses, back lighting for illumination, and Halcon image processing software.
Additionally, a sensor has been used to send image capture signals to the camera. We simulated shampoo movement on the production line using a conveyor belt and utilized a Delta PLC and alarm light to display the results of shampoo image processing. Below, you’ll see the necessary equipment.
Communication Method among Machine Vision System Components in Label Quality Control
The practical Halcon software connects to various industrial cameras. Here, we’ve utilized a GigE camera connected to Halcon via a network cable. Moreover, under the Modbus protocol, we can connect Halcon to the PLC via a network cable. On one end, the sensor is connected as input to the camera, and the alarm light as an output to the PLC. We’ve extensively explained the details of machine vision equipment and their connections in the Halcon machine vision training.
Functioning of Machine Vision System in Label Inspection
Our goal is to detect the presence or absence of a label on the product. As the shampoos pass in front of the camera on the conveyor belt, the sensor sends image capture signals to the camera. The camera captures the image, and the Halcon software detects the presence or absence of a label through image processing. In case of label absence, the program sends a signal to the PLC to command turning on the alarm light.
Software Concept for Quality Control of Labels on Products
As mentioned, we use Halcon image processing software to process images. Since back lighting is used in this project, parts of the image containing the label are darker. Therefore, by examining the brightness level of pixels within a defined range, the label area becomes detectable. For more information on the pixel count, see the Histogram Drawing with Halcon article.
Displaying Results in the Label Inspection Program
With image processing from the camera, if the label is absent within the defined area, that area is marked with a red box on the monitor, and the message “NOT GOOD” is displayed at the top of the image. Simultaneously, the software turns on the alarm light through the PLC.
On the production line, instead of turning on the alarm light, the PLC activates the defective product rejection section. If the label is present, the relevant area is displayed with a green box and the message “GOOD” is shown at the top of the image.
Implementation of Quality Control Projects at Machine Vision Company
Apart from industrial projects, Visions Systems has implemented various experimental projects in line with its educational goals. Some similar projects include packaging inspection, checking liquid height in bottles, defective print inspection and rejection, and more. In the image below, from right to left, liquid height inspection and bottle cap print inspection with machine vision have been performed.
As seen in the image, other inspections such as barcode, date and price verification on the product, label integrity, open or closed bottle caps, label placement, etc., can also be done using vision systems. In the Halcon machine vision course, we teach you how to design and implement a vision system using Halcon software.
Related Articles